Der Zylinder und die Schnecke bilden das Extrusionssystem, die beide unter hohen Temperaturen, hohem Druck, starker Reibung und bestimmten Korrosionsbedingungen arbeiten. Gleichzeitig hat der Zylinder auch die Aufgabe, Wärme auf das Material zu übertragen oder dem Material Wärme zu entziehen.
Struktur des Fasses:
Die Fassstruktur kann entweder integriert oder montiert sein:
- Integral Barrel: Der integrierte Zylinder wird aus einem einzigen Knüppel gefräst. Diese Struktur zeichnet sich dadurch aus, dass sie eine hohe Fertigungs- und Montagepräzision gewährleistet, eine gleichmäßige Beheizung ermöglicht und den Auf- und Abbau des Heiz- und Kühlsystems vereinfacht.
- Zusammengebauter Lauf: Das zusammengesetzte Fass setzt sich im Allgemeinen aus mehreren Fasssegmenten zusammen. Im Vergleich zum integralen Fass ist es einfacher zu bearbeiten und kann je nach den verschiedenen Nutzungsanforderungen und Produkttypen angepasst werden. Allerdings erfordert dieser Aufbau eine höhere Bearbeitungsgenauigkeit. Bei zusammengesetzten Zylindern werden häufig Flansche und Schrauben zur Verbindung der Segmente verwendet, was die Gleichmäßigkeit der Erwärmung beeinträchtigt, den Wärmeverlust erhöht und die Einrichtung und Wartung des Heiz- und Kühlsystems erschwert.
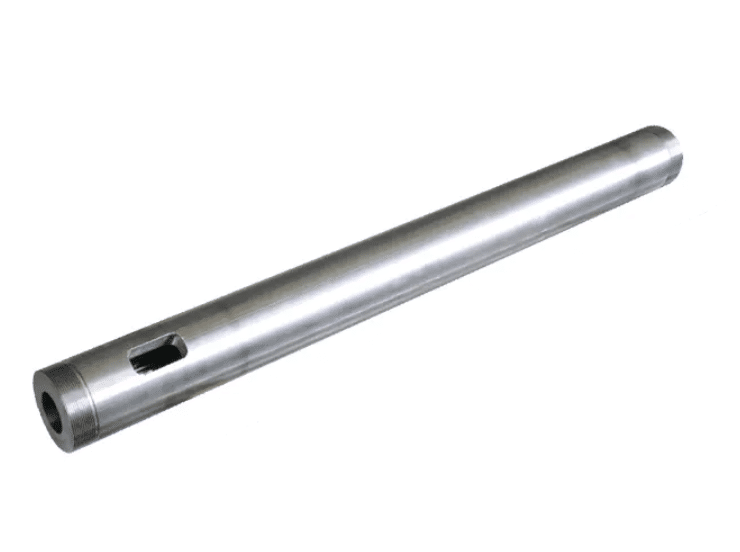
Materialien des Fasses:
Zu den Trommelmaterialien gehören in der Regel legierte Stähle wie 30Cr und 38CrMoAl. Auch Kohlenstoffstahl oder Gussstahl kann als Grundmaterial verwendet werden, wobei zur Verbesserung der Verschleißfestigkeit eine Einlage aus legiertem Stahl eingebettet wird.
Formen des Einzugsbereichs des Fasses:
Herkömmliche Extruder verwenden in der Regel die folgenden beiden Methoden zur Verbesserung der Feststoffförderleistung:
- Längsrillen: Bearbeitung der Längsrillen an der Innenwand des Einzugsbereichs des Laufs.
- Verjüngter Abschnitt: Das Fass in der Nähe des Trichterteils wird konisch.
Längsnuten im Kopf der Maschine können nur in dem Bereich bearbeitet werden, in dem das Material noch fest ist oder gerade zu schmelzen beginnt. Die Länge der Nuten beträgt in der Regel etwa das 3~5-fache des Durchmessers (D). Die wichtigsten Daten für die Bearbeitung von Längsnuten in gängigen Extruderzylindern sind in der nachstehenden Tabelle aufgeführt.
Die Länge des Kegels an der Innenwand des Zylinders beträgt in der Regel das 3 bis 5fache des Durchmessers (D). Die Größe der Verjüngung hängt von der Partikelgröße des Materials und dem Durchmesser der Schnecke ab; die Verjüngung nimmt mit zunehmendem Schneckendurchmesser ab.
Form und Position der Einspeiseöffnung:
Die Form und Position der Zuführungsöffnung am Fass haben einen erheblichen Einfluss auf die Zuführungsleistung. Die Zuführungsöffnung sollte es dem Material ermöglichen, effizient und ungehindert in den Zylinder zu gelangen, ohne dass es zu Brückenbildung kommt. Außerdem sollte sie das Einrichten des Kühlsystems erleichtern. Die Form der Einfüllöffnung kann rund, quadratisch oder rechteckig sein, wobei die rechteckige Form bei Extrudern am weitesten verbreitet ist.